Phoenix 3D Printing isn’t your granddad’s daisy wheel or mom’s dot matrix. It’s advanced technology that builds three-dimensional objects, and it’s now on shop floors, design studios, rec rooms, and kitchen tables worldwide.
Designers use them to quickly produce product models and prototypes. They’re also used to make end products such as tools, tripods, and gifts.
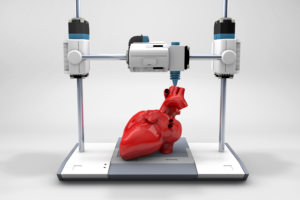
The short answer is that 3D printing is a process of layering material to build up a three-dimensional object according to a digital model. It is also known as additive manufacturing, as it adds material rather than cutting off existing material, as in subtractive processes like machining.
The longer answer is that 3D printing has been used for rapid prototyping, producing parts and prototypes from CAD models in a fraction of the time required using traditional methods. Engineers can turn a CAD file into a physical part within hours, and then test that part and make necessary adjustments before moving to the next phase of design.
It is also increasingly being used for end-use production, and for creating specialized tools, molds and manufacturing aids. The ability to create parts from a wide range of materials, including metals and plastics, opens up many new possibilities for product designs. There is even scope for producing parts from specially tailored materials to provide specific functionalities such as heat resistance or greater strength in certain applications.
In addition to being more cost-effective and speedy than traditional methods, 3D printing also produces more accurate parts, enabling companies to produce high-fidelity proof of concepts and prototypes that look, feel and work just like the final products. This enables engineers and designers to create complex, bespoke shapes that would be impractical or impossible to manufacture using traditional methods.
3D printing can also reduce the number of components in a product, reducing assembly time and improving its performance and reliability. It can also help to consolidate assemblies into smaller parts, alleviating weak points and reducing weight. The emergence of ceramic printing technology means that intricate, organic shapes and textures can now be created in 3D, opening up a host of new opportunities for design and engineering.
Medical-related 3D printing is an important area of growth, allowing physicians and technicians to produce patient-specific replicas of bones, teeth and organs for planning surgery and medical treatment. Some patients are already benefiting from 3D-printed prosthetics and hearing aids, and printers that can use living cells to create artificial organs are on the horizon.
3D Printing Materials
3D printing can be used to print a wide range of materials, from plastics and metals to ceramics and even human bone. The most common printing materials are thermoplastics, which become soft and moldable when heated and return to their solid state when cooled.
There are several different 3D printing processes, each using a different material. Some 3D printers use a laser to selectively melt powdered material in a layer-by-layer process, while others fuse parts together using heat, electricity, or radiation. The most popular 3D printing method is a material extrusion technique called fused deposition modeling (FDM). FDM uses melted thermoplastics that are squeezed through a nozzle onto a build plate, one layer at a time.
Another 3D printing technology is material jetting. This method uses a jet of UV light to cure photopolymers, which are used as the building blocks for the final part. This type of 3D printing is a good option for creating full-color, transparent, or translucent parts that are lightweight and durable.
Binder jetting is another 3D printing technique that is similar to inkjet printing. It uses a head that moves over the platform base to spread and deposit alternating layers of powdered materials and a binding adhesive agent. The resulting “green” state part is then cured and sintered. This type of 3D printing is well suited to producing a wide range of functional prototyping parts, including castings and tooling.
A third category of 3D printing material is composites, which combine multiple materials to achieve the desired properties. For example, a filament like Markforged’s Onyx combines nylon with chopped carbon fiber to make the part stronger and lighter. Other examples of composites include fillers such as wood, sand, or clay, which give the finished product texture and strength, or metals, which provide strength and stiffness.
The most common 3D printed products are polymeric, but the technology is rapidly evolving to incorporate other materials such as metals and ceramics. Moreover, the technology is not only revolutionizing industrial production but also enabling the emergence of new forms of manufacturing that are more responsive to local needs. For instance, a London design firm has used a massive 3D printer to build comfortable dwellings in days for families unhoused by recent natural disasters.
3D Printing Software
3D printing has revolutionized manufacturing, making it possible to print on-demand parts for consumer electronics and other products, and allowing personal creativity to expand with the ability to make prototypes quickly. As the technology grows in popularity, manufacturers are working to improve performance and expand the materials available for printing. This means that 3D printers are now able to print in plastics, metals and other materials not previously available to consumers, opening up possibilities across multiple industries.
A variety of software is available to aid in the process of designing, preparing and managing your 3D printing projects. This includes slicer software, which converts the digital model into instructions that your printer can understand. Some of this software also offers other functions, including design and digital sculpting tools.
One of the most popular slicing software options is Cura, which has become the standard for many desktop 3D printers. Designed by Ultimaker, this free program has a user-friendly interface that allows you to customize your prints to the specifications of your machine and features advanced visualization capabilities. The program is easy to use and includes a vast online community for troubleshooting and tutorials.
Another slicing software option is Repetier, which was developed by the creators of the original Prusa 3D printer. This open-source software allows you to adjust the settings for your specific 3D printer, and offers real-time incremental slicing. This means that when you change a setting, the entire print does not need to be recalculated; only the affected areas are resliced.
Other 3D printer software options include Blender, which is a versatile 3D modeling and animation tool with a wide range of tools, including a digital sculpting tool. Its robust library of models and community resources makes it a great choice for both novices and experts alike. While it has a steeper learning curve than some other software, its versatility and extensive feature set make it a favorite for professionals and hobbyists alike.
Autodesk Fusion 360 is a CAD program that combines parametric, surface, and freeform direct modeling. It’s ideal for complex mechanical designs and provides a unified design platform, which allows team members to work together in real time. This 3D software is also available as a cloud-based option, allowing users to collaborate and share files with ease.
3D Printing Process
The 3D printing process transforms digital files containing three-dimensional data—whether created on a computer-aided design (CAD) or computer-aided manufacturing (CAM) program or from a 3D scanner—into physical objects. It is considered an additive process because it builds up layers of material rather than cutting or milling it away as in traditional subtractive manufacturing.
There are several different types of 3D printers, and each works a little differently. Most of them work by exposing a liquid polymer to light in order to harden it layer-by-layer, based on instructions from CAD or CAM software. This is called vat photopolymerisation and the most common method is stereolithography, often abbreviated as SLA. It uses a UV laser beam that shines into a container of photopolymer resin and solidifies it wherever it touches. Other methods include digital light processing (DLP) where a projector emits a pattern of light onto the surface of liquid polymer and also direct energy vat photopolymerisation which is similar but uses an electron beam instead of a laser.
Many of the same considerations that apply to other types of manufacturing apply to 3D printing:
- Intellectual property rights.
- The need for proper ventilation and a safe workspace.
- The fact that some of these processes can generate toxic fumes.
The use of extractors and the adherence to correct procedures can prevent these issues.
3D printers are most often used for rapid prototyping, but this technology can be applied to the production of end-use parts as well. For example, automotive companies have embraced the ability to print spare or bespoke parts as they need them and in this way shorten their product development cycle. In addition, manufacturers can produce jigs and fixtures or small batches of end-use products with this technology.
The choice of which 3D printing process to use will depend on the desired material, mechanical properties and build size. To help with this, our guide to Selecting the Right 3D Printing Process can provide guidance. In terms of materials, each process is compatible with a range of different plastics, metals and ceramics.